Cape Town City Hall
The Restoration of the Cape Town City Hall tower clock. The clock is a 50% scale replica of Big Ben and was installed in the 1900’s. Over the years the clock has been worked on but a full restoration had not been done for years. The main reason for the restoration was the old grease and oil that was impregnating the gear teeth. This can cause excessive ware on both gear teeth and pinions. The process was similar to the work done on the V&A Tower Clock except the frame was left on site and the gears, bolts and all working parts were refurbished in the building. We set up a temporary spray boot, polishing station and sand blasting booth. Here is a breakdown of the process.
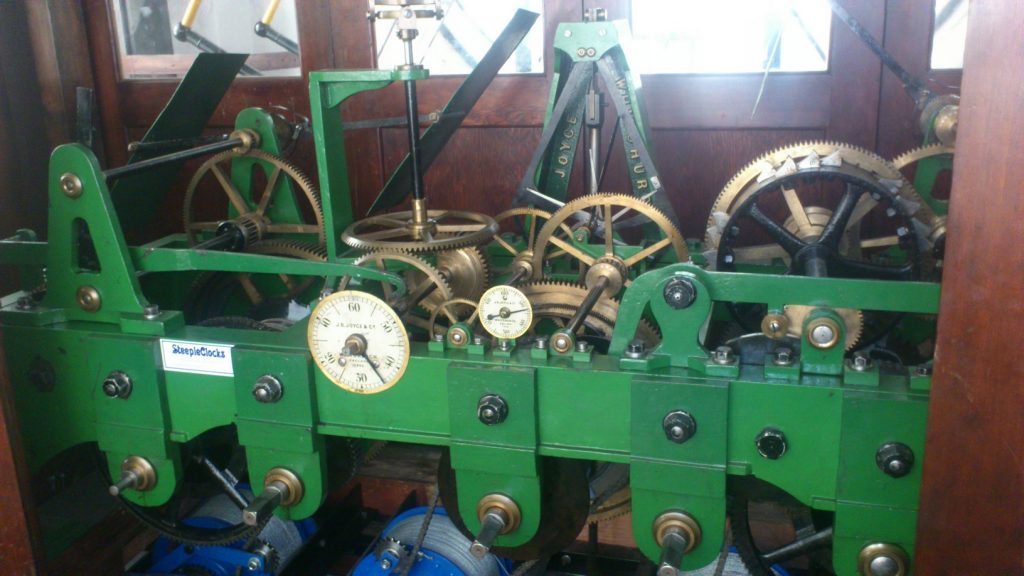
All gears, bolts, levers, barrels and pins were removed and stripped firstly in an industrial de-greaser. The parts were then sandblasted to remove all debris and old paint.
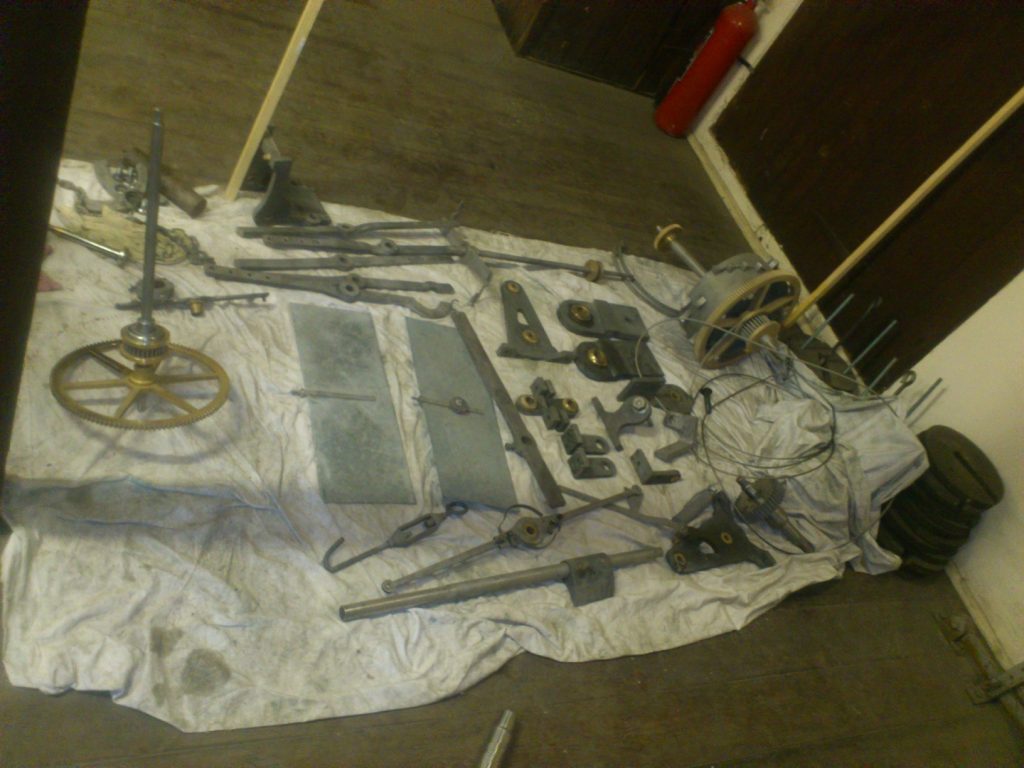
All the phosphor bronze gears and parts were stripped of old grease/oil and polished. The polishing process is done on a polishing machine where the gears are polished with various buffing wheels and pastes. The rough buffs and pasts are used first and then a mid range and then eventually a fine paste and buffing wheel.
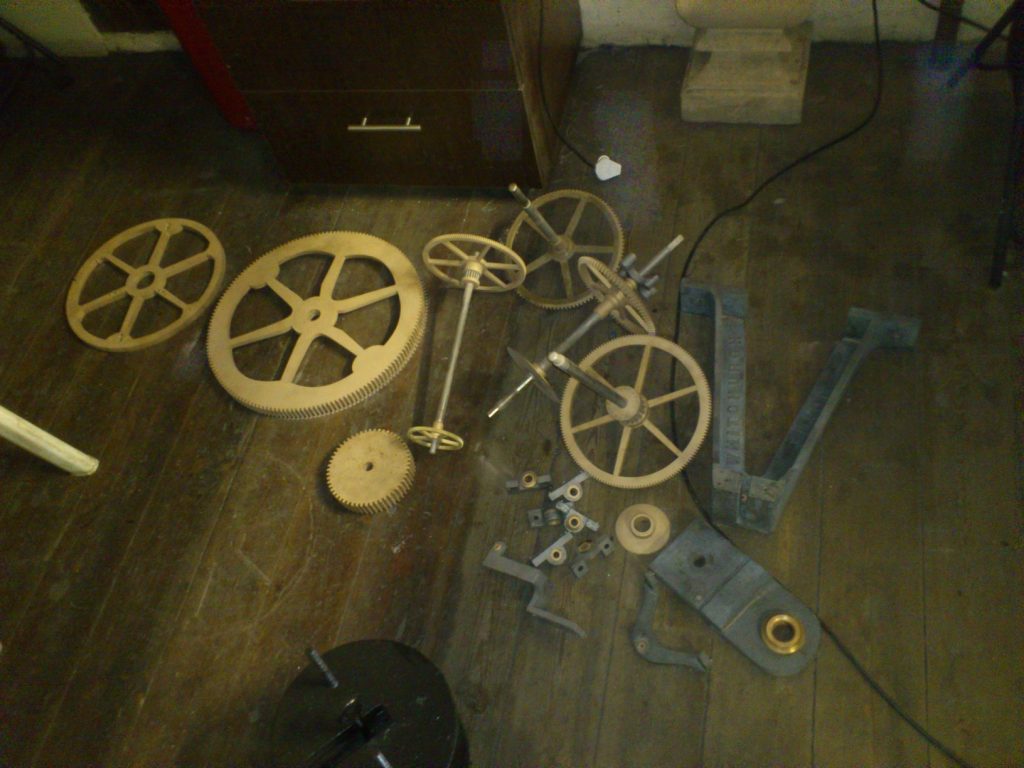
As this is a public clock I was asked to keep the clock running for as long as possible during the refurbishment so the going train was left running while the other sides were being refurbished. One of the barrels of the mechanism had broken teeth. The clock has a self-winding system installed do it was set to work off some of the teeth that were not damaged but we decided to have them repaired while the clock was dis assembled. This was done by having a new ring of teeth cut with a water jet cutter. The old teeth were then removed on a lathe and the new ring of teeth was fitted and secured with countersunk screws.
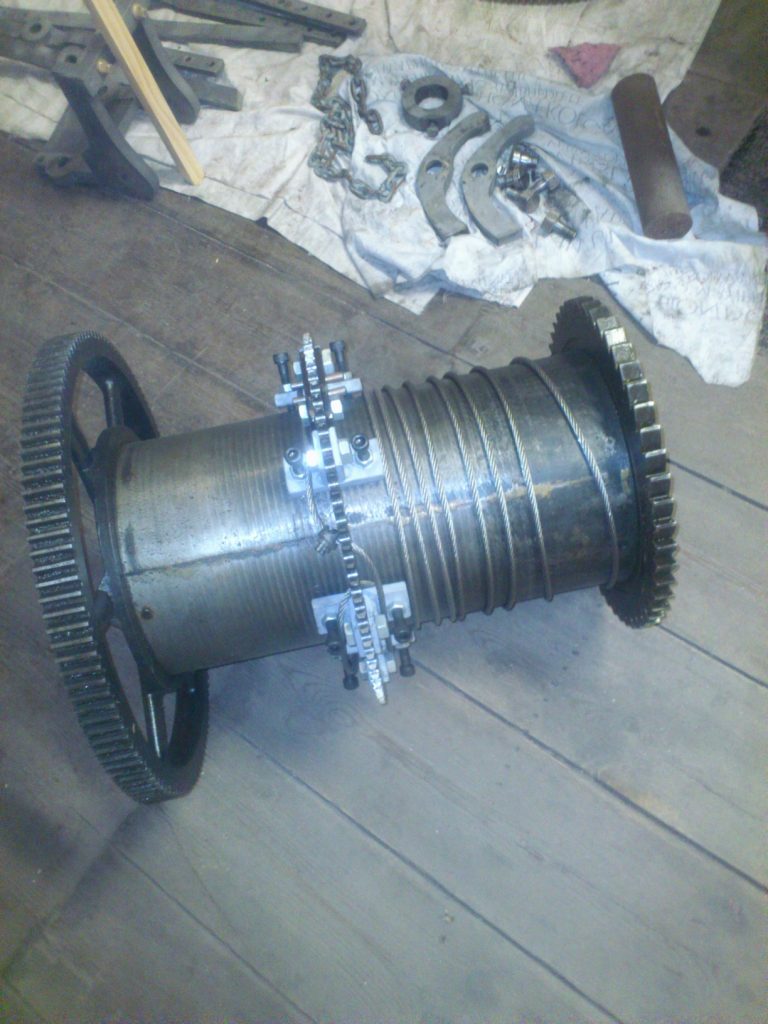
All the bolts, pins and screws were blued. The bluing process is to bed the metal into a layer of brass filings. This is to distribute the heat evenly. Metal changes color when heated and blue is a very early stage of the heat process. The cleaner the metal the better the result. The metal is then dropped into oil this stops the heat from transferring and also causes the oil to penetrate the metal this creates a layer which prevents future corrosion. In this case all parts except the gear shafts were blued.
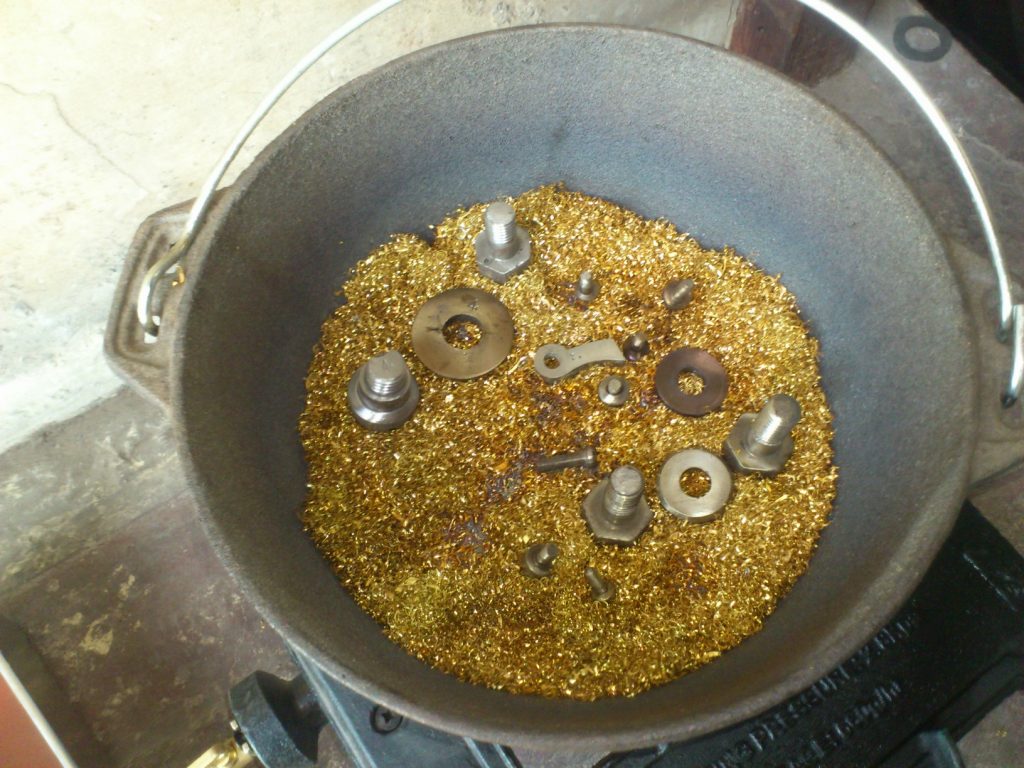
After the strike and chime systems were re-assembled and installed the same process was done with the going side. As before we tried to keep the clock running as much as possible during the restoration. This side was stripped, refurbished and re-installed in 1 week. The frame of the clock was stripped of old paint and repainted. This was done in sections as the parts were removed. The paint used was DTM (direct to Metal) which had to be mixed to match original color.
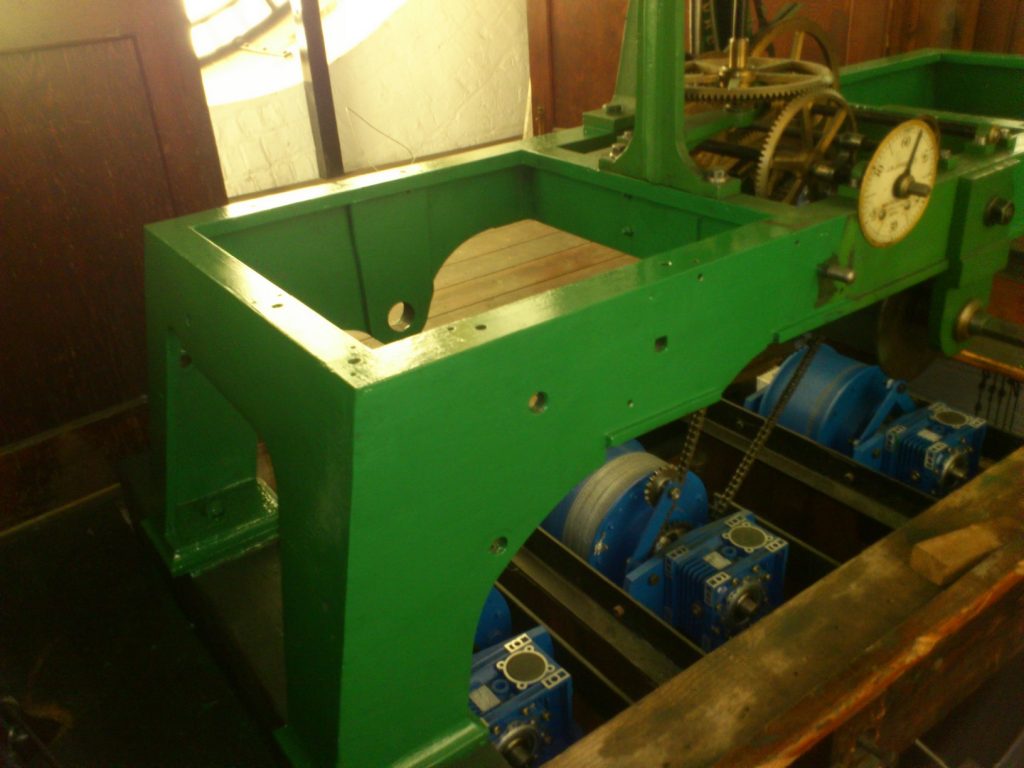
The next phase of the project was to restore the top section of gearing. This section consists of the gears that sit above the clock and lead to the gears which run the hour and minute hands. As before they were stripped, sandblasted and refurbished. All the metal supports and bushing bars were also refurbished and repainted. At this stage the we had scaffolding erected and the hands were removed. The hands were repainted and while the scaffolding was up the dials were given a coat of paint.
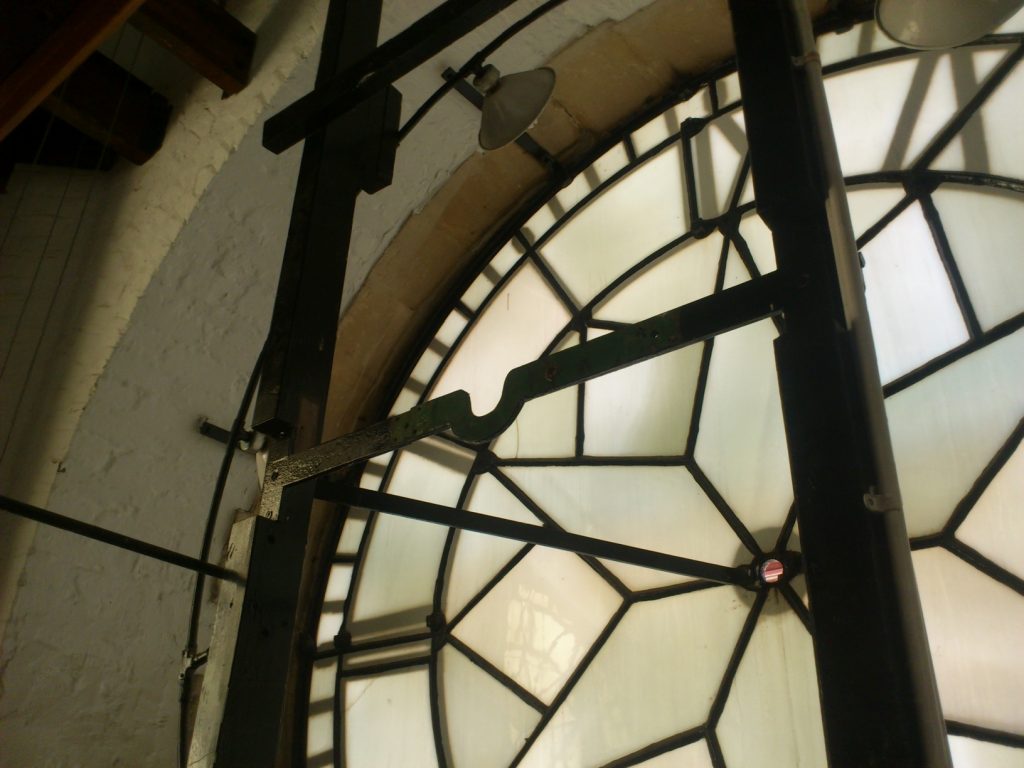
The clock is now completely refurbished and running perfectly